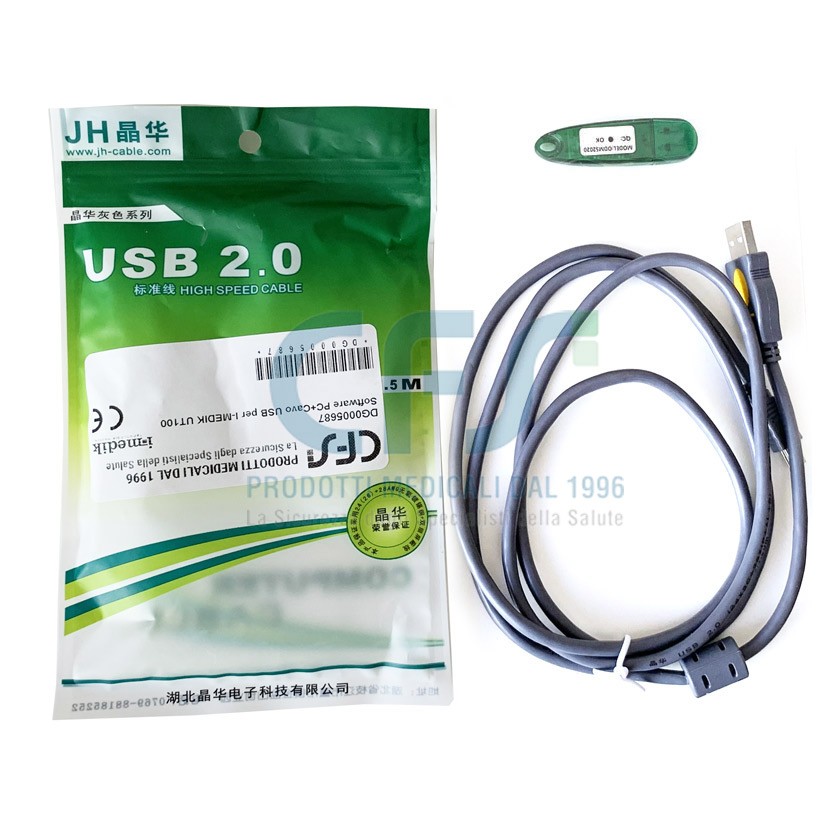
Saturimetro palmare I-MEDIK UT100 con Software + Caricabatteria e Guscio Omaggio su CFS PRODOTTI MEDICALI

medisana PM 100 pulsossimetro misurazione della saturazione di ossigeno nel sangue, pulsossimetro a dito con display OLED e funzionamento one-touch : Amazon.it: Salute e cura della persona
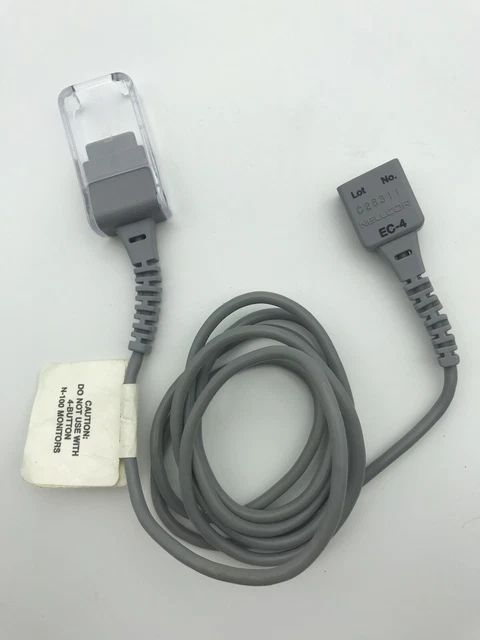
NELLCOR CAVO ESTENSIONE EC-4 Prolunga Pulsossimetro Saturimetro SpO2 Ossigeno EUR 9,99 - PicClick IT
